CODACA's automotive grade inductors assist in the innovation of automotive lighting products, effectively enhancing driving experience and safety
Car lights are one of the most important components of a car. With the development and improvement of LED lighting technology, as well as the pursuit of safer lighting environments by car users, car lights provide more functions in terms of safety and experience. In addition to the traditional lighting function, many new car models also have lighting systems that automatically turn on, adjust height and brightness, follow the steering, and switch between high and low beams, effectively improving the driving experience and safety.
Car headlights include headlights, fog lights, reverse lights, etc. Among them, headlights are very important lighting components for cars driving at night. Car designs usually use the same control circuit to drive all headlight functions, such as low beam, high beam, daytime running lights, and cornering lighting.

A lot of power inductors are used in the VRM circuit of the DC-DC converter for LED headlight driving power supply. Due to the complex application environment of automotive electronics, inductor products need to be resistant to high currents, high and low temperatures, mechanical vibrations and impacts, and possess features such as compact design, lower losses, and better DC bias characteristics.
1. The requirements for inductor in the driving power supply of car lights
◾ High and low temperature resistance: The car lamp circuit board is located in a closed installation space with poor heat dissipation conditions. The temperature near the headlights is very high, and the inductor needs to withstand high temperatures of up to 100 ℃. Some traditional halogen and xenon lamps operate at even higher temperatures. In addition, in some extremely cold regions where the temperature is below -40 ℃, the inductor must be able to withstand the test of low-temperature environments.
◾ High current: The electronic circuit of car headlights belongs to a high-power design scheme, and the inductance must maintain sufficient inductance value under high transient peak current conditions to ensure the normal operation of the circuit. At the same time, it also needs to withstand continuous high current output for a long time to maintain the surface temperature rise of the inductor not exceeding the specified value, which can avoid the long-term high temperature affecting the life of the inductor or burning out the inductor, causing car lamp faults.
◾ Low loss: The working frequency of the car light scheme design is relatively high, and the inductance adopts low loss magnetic core material, which can effectively reduce high-frequency magnetic core loss, reduce the heat generation of the car light, achieve energy conservation and environmental protection, and improve output efficiency.
◾ High reliability: As a means of transportation, cars need to maintain good performance in various environments, such as harsh weather conditions, high and low temperature differences, and high vibrations. Therefore, there are high requirements for the material characteristics, product structure, and production process of electronic components. Inductive products not only need to be able to resist impact and mechanical vibration, but also maintain good electrical performance in high and low temperature environments.
◾ Anti interference: The PCB board in the headlight area occupies limited installation space, and components require high-density installation, which inevitably leads to various electromagnetic interference problems. The use of magnetic shielding structure design can improve the shielding effect of inductors and effectively reduce electromagnetic interference.
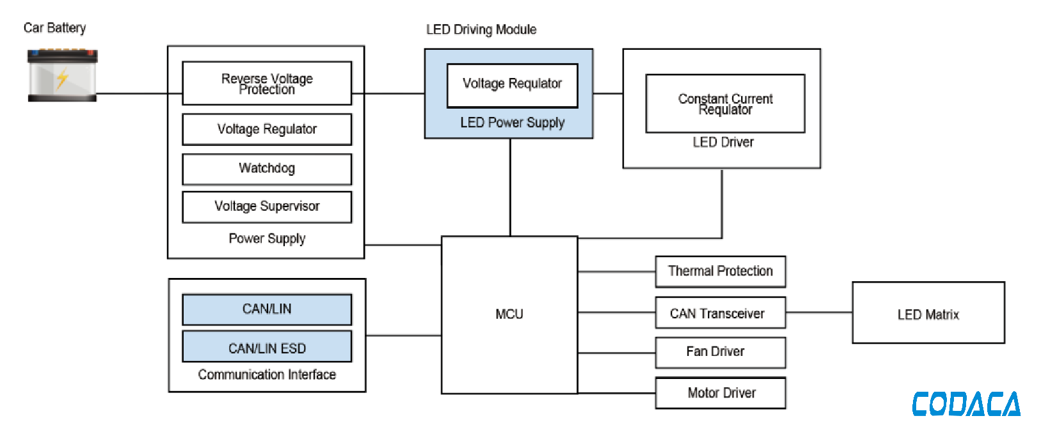
Fig.1 Application Block Diagram of Inductance for Automotive LED Light Driver Module
2. Solution for Automotive Lamp Drive Power Inductor
In response to the application requirements of automotive headlights, CODACA works closely with automotive electronics engineers to independently develop and design the VSHB, VSHB-T, VSAB, VSEB-H series of automotive grade integrated inductors that are resistant to high temperatures, high currents, low losses, and high reliability.
The CODACA automotive grade molded inductor is made of low loss alloy powder, which has the characteristics of minimum power consumption and lowest DC resistance in the same size. The alloy powder core has the advantage of high Bm value, which makes the product have better DC bias capability. The product adopts a fully magnetic shielded structure, which has strong anti electromagnetic interference ability. The close combination of coils and magnetic cores can effectively avoid the occurrence of noise and withstand high-intensity mechanical impacts and vibrations. In addition, the small volume packaging size design is suitable for high-density installation.
CODACA's automotive grade molded inductors have passed the AEC-Q200 Grade 0 reliability test and have excellent reliability, ensuring long-term stable operation of the product in complex environments.
2.1 Automotive grade Molding Power Chokes VSHB series
The CODACA automotive grade molding power chokes VSHB series is made of low loss alloy powder, which has the characteristics of low loss, high efficiency, and wide application frequency. The working temperature ranges from -55 ℃ to+155 ℃.


2.2 Automotive grade Molding Power Chokes VSHB-T series
The CODACA automotive grade molding power chokes VSHB-T series adopts a cold and hot pressing two-stage molding process and a T-Core magnetic core structure design, effectively reducing magnetic core losses and minimizing short-circuit risks. The innovative T-core magnetic core structure ensures the reliability and consistency of the electrical performance of the inductor by preventing deformation and tilting of the inductor coil. The working temperature range of this series of products is -55 ℃ to+165 ℃, reaching the highest level in the industry.


2.3 Automotive grade Molding Power Chokes VSAB series
The VSAB series of automotive grade molding power chokes adopts an integrated structure with ultra-low buzzing noise. Specific mixed powder design with outstanding voltage resistance. Magnetic shielding structure with strong resistance to electromagnetic interference. The lightweight design can save installation space and is suitable for high-density mounting. The working temperature range is -55 ℃ to+155 ℃.
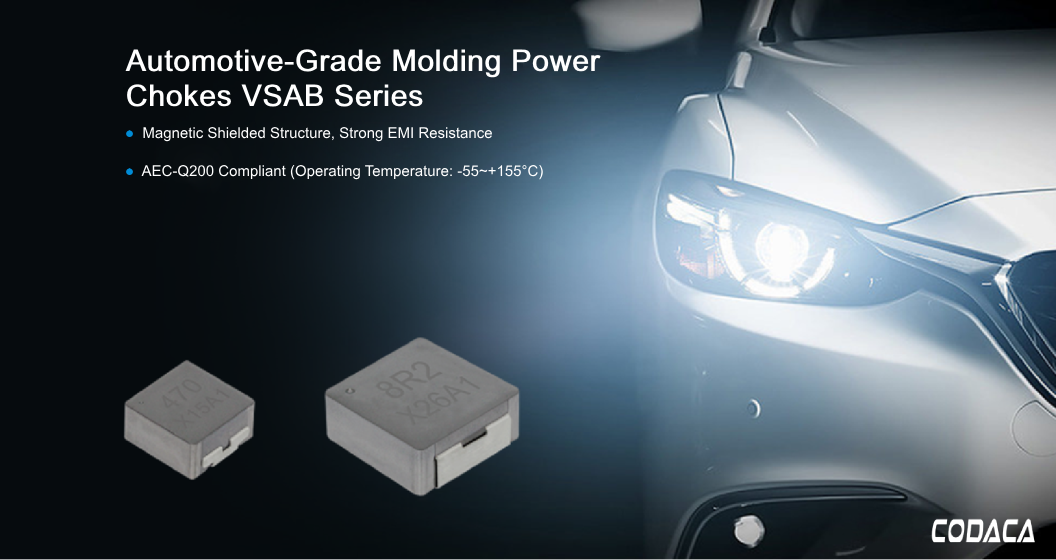
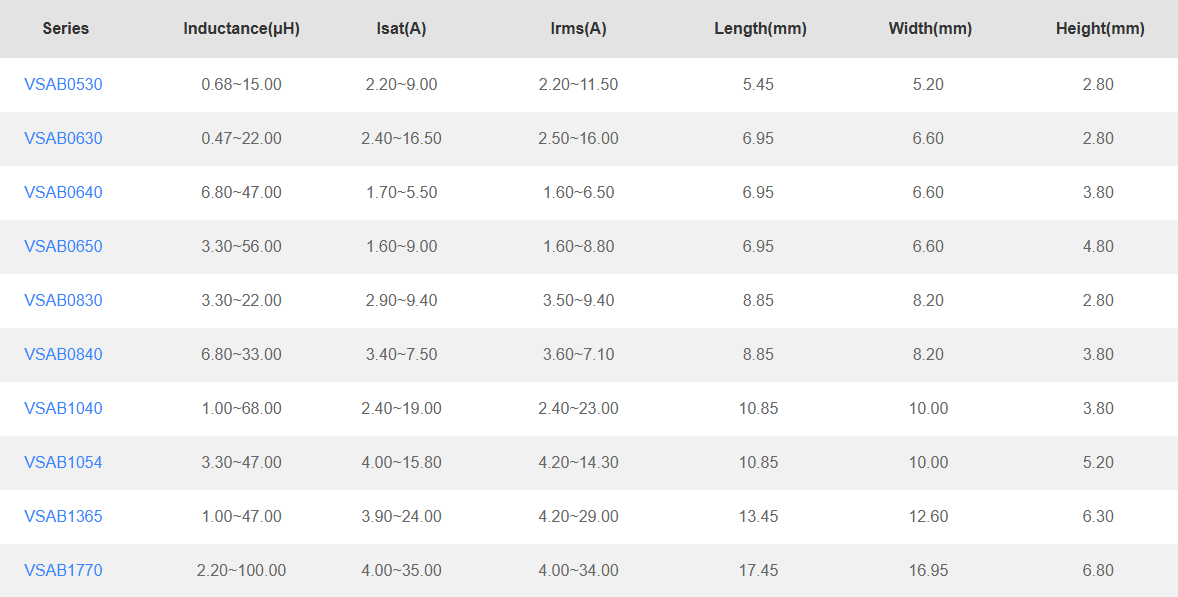
2.4 Automotive grade Molded Power Inductor VSEB-H series
The VSEB-H series of automotive grade molded inductors adopts hot pressing integrated molding technology and T-Core magnetic core structure. It has the characteristics of low loss, wide application frequency, high reliability, and high operating current. Lightweight design, saving space. The working temperature range is -55 ℃ to+155 ℃.

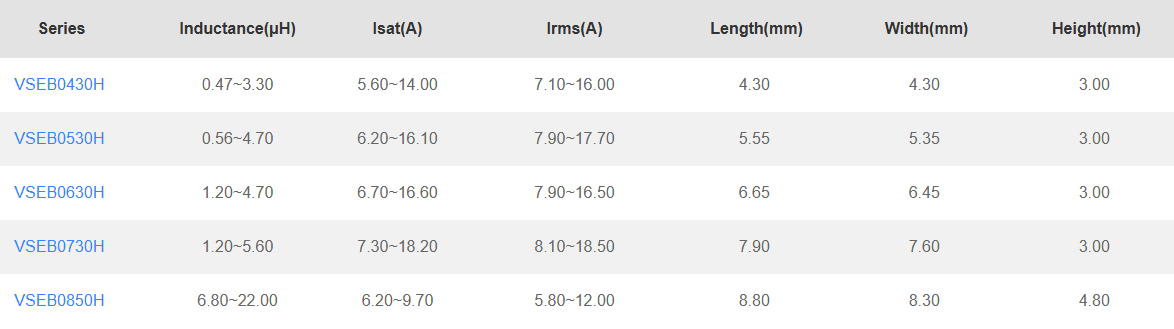
3. More automotive grade inductor solutions
For automotive electronic applications, CODACA Electronics has independently developed multiple series such as the automotive grade high current inductor VSRU27 and the automotive grade magnetic rod inductor VRKL0740. Automotive grade inductors are widely used in various automotive electronics such as intelligent cockpits, advanced driving assistance systems, central control units, headlight drive modules, car entertainment audio systems, BMS, T-BOX, etc.
As a professional manufacturer of molded inductors and high current power inductors with 24 years of experience in power inductor development, in addition to providing standard products, CODACA Electronics also has strong product customization capabilities. The core material of the inductor is independently developed and can be quickly customized according to customer needs and different application scenarios. The automotive grade inductors are manufactured in factories certified by IATF16949, and the company has a CNAS accredited laboratory that can test according to the AEC-Q200 passive component product validation standard.