Innovative production process to achieve low loss and high reliability of VSHB series integrated inductors for automotive grade
With the integration and intelligence of automotive functions, how to achieve optimal inductor product performance within limited packaging size, how to achieve low loss and high reliability of automotive grade inductor products through technological innovation, and ensure the continuous and stable operation of automotive electronics in complex environments have become challenges for inductor manufacturers.

Taking the production and manufacturing of room temperature molded inductors as an example are formed by high-pressure, which makes it easier for the internal coils of the product to deviate, resulting in abnormal cracking risks. This is very unfavorable for automotive electronic products with high reliability requirements. The use of low-pressure hot pressing technology can fundamentally solve the risk of cracking caused by coil displacement, and effectively improve the reliability, magnetic powder density, and electrical performance of automotive grade integrated inductors.
1. Room temperature pressed molded inductor vs. hot pressed molded inductor
Room temperature pressed and hot pressed methods are two kinds of production methods in which spot welded semi-finished products and finished powder are integrated into a mold during the production process.
Among them, room temperature pressed method is currently the most common production method for integrated inductors, which is carried out at room temperature of 25 ℃ and pressure is often between 5.0~9.0 T/cm2. The contradiction between the magnetic powder density, product characteristics, and coil inclination/deformation of the inductor has been unable to be effectively balanced by using the room temperature pressed molding method.
Hot pressing refers to the process of controlling temperature and pressure to achieve integrated forming of inductors through powder casting, connection, and packaging at high temperatures (usually above 100 ℃) and low pressures. Hot pressing has low molding pressure, and the pressure that the coil withstand is only 35% - 48% of traditional room temperature pressing technology, greatly reducing coil deformation, improving the reliability and stability of the circuit, and also significantly reducing the overall loss of inductance. However, the hot pressing method has high requirements for the characteristics of magnetic powder and the production process of manufacturers, so it has not been widely used at present.
Through years of technical research, CODACA Electronics has mastered the independent development technology of magnetic core materials and the production process of hot pressed integrated inductors, and has applied it to the research and production of automotive grade molded inductors. Its representative products mainly include automotive grade Molding Power Choke VSHB, VSHB-T, VSEB-H and other series.

Vehicle grade Molding Power Choke VSHB series
2. Low loss alloy powder+hot pressing integrated molding technology effectively improves the reliability of automotive grade inductors
The CODACA car grade integrated molded inductor VSHB series adopts self-developed low loss high-frequency alloy powder, which has low loss, high efficiency, and wide application frequency. The introduction of low-pressure hot pressing technology in the production and manufacturing of inductors allows for a more thorough bonding between resin and magnetic powder compared to conventional cold pressing, greatly enhancing the strength and density of the powder. Due to the significantly lower pressure of hot pressing compared to cold pressing, it can effectively reduce the deformation and misalignment of the internal coils of the inductor, fundamentally solving the problem of product cracking.
Due to the use of hot pressing integrated molding technology and CODACA's independently developed low loss magnetic core, the VSHB series inductors have higher reliability, stronger density, and superior electrical performance.
The comparison of the characteristics between traditional cold pressing technology and VSHB series innovative technology (hot pressing) is shown in Table 1.
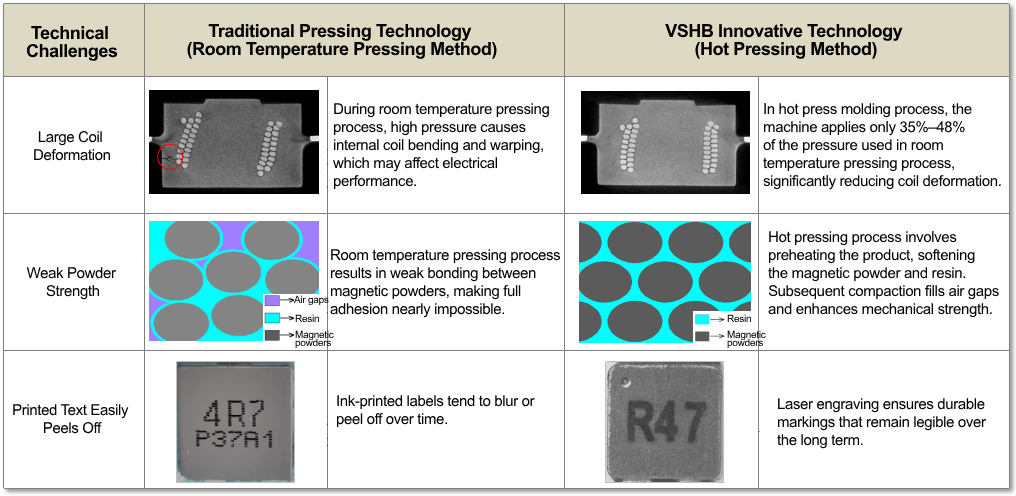
Table 1: Comparison between Traditional Room Temperature Pressing Technology and Innovative Hot Pressing Technology
3. Advantages of VSHB series products
3.1 Product Features
● Independently developed low loss high-frequency alloy magnetic powder;
● Low loss, high efficiency, wide application frequency;
● Lightweight design, space saving, suitable for high-density mounting;
● Wide terminal structure improves the anti vibration performance of inductors;
● Working temperature: -55 ℃ to+155 ℃, reaching the international advanced level.
3.2 Product advantages
Compared to traditional integrated room temperature pressing technology products, the VSHB series hot pressing product inductors have the following characteristics:
● Extremely low DCR, with a decrease of approximately 45% to 60% in DCR
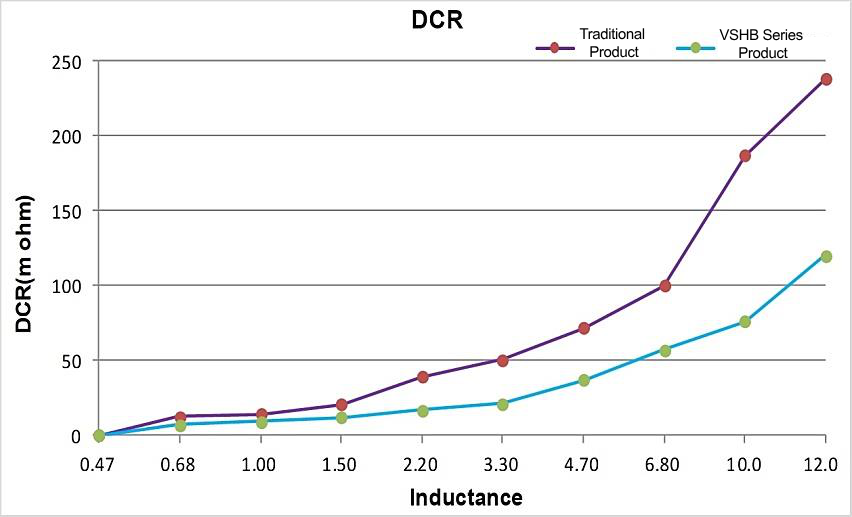
Comparison of DCR Trends
● Better saturation current characteristics
Small size, high current. The maximum saturation current can reach 14.5A.
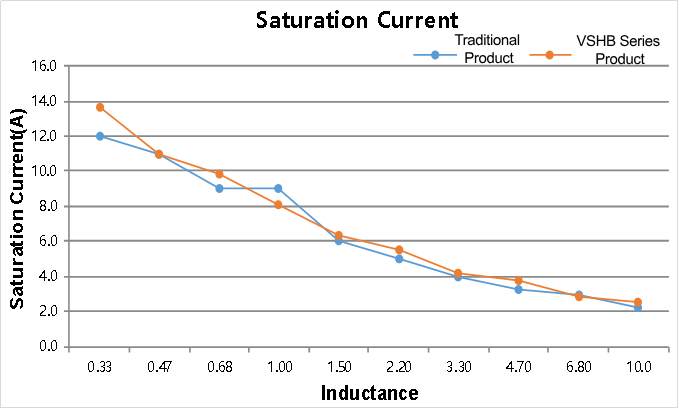
Comparison of saturation current curves
● Lower losses, overall inductor losses can be reduced by 30%
Through testing, it has been found that the overall loss of the integrated inductor using innovative hot pressing technology is 20% to 30% lower than that of traditional technology, greatly improving the efficiency of the product in the circuit.
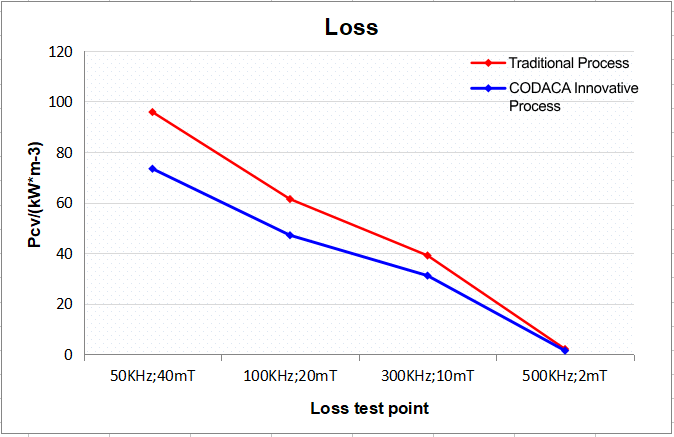
Comparison of inductance losses
● Higher reliability, widely applicable in various fields
The working temperature of VSHB series inductors is -55 ℃ to +155 ℃, suitable for high frequency and high temperature environments. It can be widely used in assisted driving systems (ADAS), information entertainment, remote monitoring (T-BOX), in car chargers (OBC), LED drivers, HUD head up display systems, various DC/DC converter power modules, etc.
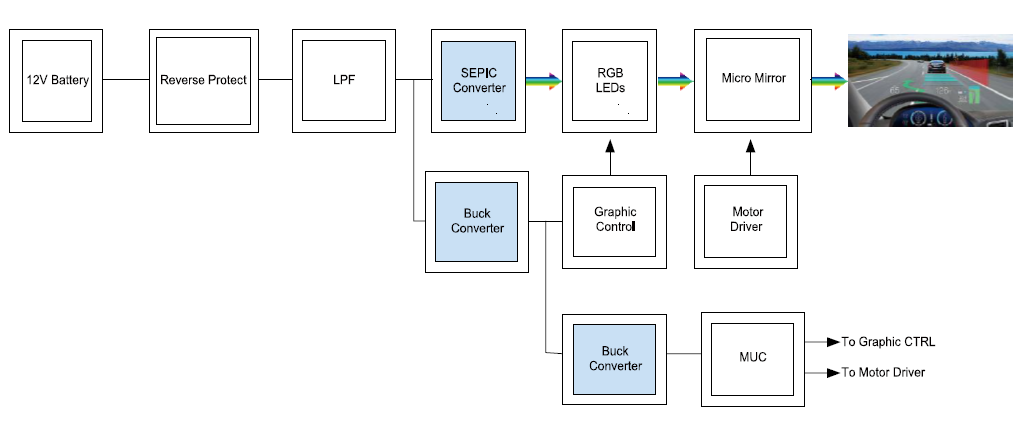
Application Example of HUD Head up Display System
3.3 Product specifications

Click on the text to request a sample
As a professional manufacturer of automotive grade inductors with a focus on power inductor research and development for 24 years, CODACA Electronics has independently developed multiple series of automotive grade integrated inductors, automotive grade high current inductors, automotive grade magnetic rod inductors, etc. Automotive grade inductors are widely used in various automotive electronics such as intelligent cockpits, advanced assisted driving systems, central control units, headlight drive modules, car entertainment audio systems, BMS, T-BOX, etc.
CODACA's automotive grade inductors are produced in modern production workshops certified by IATF16949 automotive quality management system. The company has a CNAS accredited laboratory that can conduct various reliability tests according to AEC-Q200 standards. Due to its independent research and development capabilities in core materials such as inductor cores and coils, CODACA can quickly customize automotive grade inductors for customers, helping to promote product innovation in the automotive industry.