Demystifying Qualcomm's Automotive Domain Controller Level 1 Power Supply Design: Schematic Design and PCB Design
The rapid development of the new energy vehicle industry has driven the explosive growth of each industry chain, automotive intelligence, autonomous driving has become the most important core competitiveness of new energy vehicles direction, to the highly integrated central brain and domain controller brings new challenges and opportunities, especially for the reliability of DC-DC switching power supply, high power density, switching power supply EMC, high efficiency, cost-effective to bring new opportunities and challenges.

Qualcomm as a supplier of intelligent cockpit domain controller, SA8155 and SA8295 occupies an important position, the central domain control SOC level 1 power supply (power supply converted from the battery input level 1) transient current, stable operating current, standby operating efficiency, cost, and the contradiction between switching power supply EMC design has become a huge challenge for BUCK power supply design. How to solve and balance these contradictions is the switching power supply architecture, power supply chips, inductors, Mosfet, capacitors manufacturers work together in the direction of technology.
In this paper, for the large dynamic switching power supply current (100-300%) automotive central domain control level 1 power supply design, to explore the design of DC-DC switching power supply, including power supply scheme, inductor, capacitor selection and other design methods, taking into account the volume, cost, efficiency, performance challenges to explore and real-world landing design.
Using the Qualcomm SA8295 domain controller as an example, this chapter discusses and implements a real-world design of a primary BUCK switching power supply.
This chapter requires a thorough understanding of the first part of the series (detailing BUCK switching power supply theory and calculations), and proceeds to design a detailed BUCK power supply based on the LM25149.
This series of articles contains three series (subsequent continuous updates):
01-Deciphering Qualcomm Automotive Domain Controller Level 1 Power Supply Design: Power Supply Design and Calculation (Published)
02-Deciphering Qualcomm Automotive Domain Controller Level 1 Power Supply Design: Schematic Design and PCB Design (this chapter)
03-Deciphering Qualcomm Automotive Domain Controller Level 1 Power Supply Design: Performance Test Measurement Analysis (to be released)
1- Design Goals and Challenges
1.1 SA8295 Transient Current Requirements

Table 1: SA8295 Power Supply Design Requirements
Note: The latest SA8295 design calls for 21A (1 NPU) and 24A (2 NPUs), which this design can cover (30A overcurrent protection)
1.2 Design objectives
This design uses the LM25149 to design the primary power supply for the domain controller, capable of supporting a transient current of 24A (100µs) and meeting the steady-state operating requirement of over 10A, achieving a balanced trade-off among size, cost, and performance.
Note: Transient current does not pose a thermal issue (for the Qualcomm SA8295, the transient current lasts only 100µs). However, large steady-state current can lead to increased temperature rise, so the impact of thermal performance must be evaluated (the design solution should be chosen based on actual environmental conditions).
2- Schematic and PCB design
2.1 Core component selection
Domain controller level switching power supply component selection criteria: performance priority, taking into account the cost, while reducing the area of the PCB; consider the BUCK switching power supply EMC issues and current loop issues, in line with the general BUCK switching power supply design theory and rules, you can refer to the general design methodology.
See Chapter 1 for details on electronic component selection and calculations (Demystifying Qualcomm Automotive Domain Controller Level 1 Power Supply Design: Power Supply Design and Calculations)
This design selects option 2 (using eight 47uF ceramic capacitors in C1210 package). The design is not limited to this selection, the product design can be adjusted according to the actual situation of the model, and design optimisation based on actual test results.
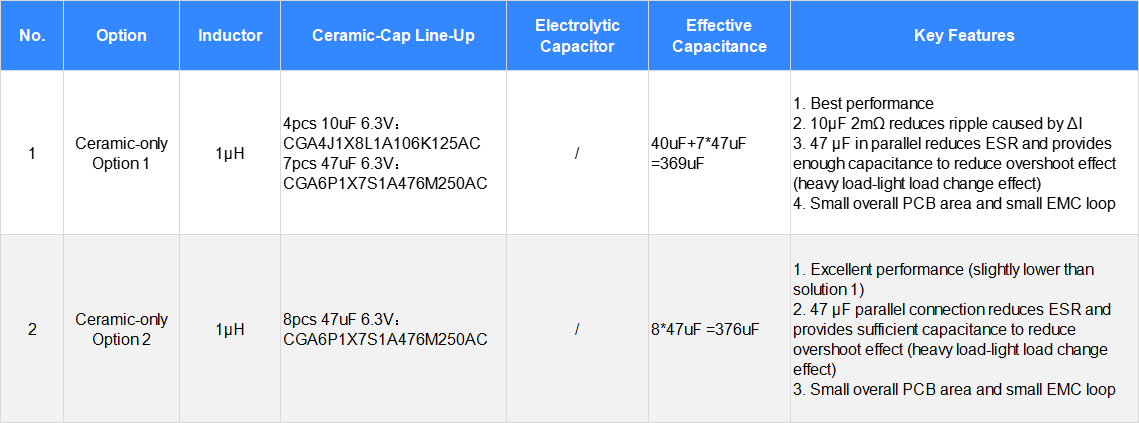
Table 2: BUCK power supply - scheme design
2.1.1 BUCK power supply-MOSFET selection

Table 3: BUCK power supply-MOSFET selection
2.1.2 BUCK power supply - inductor selection
Inductor selection using the model number: VSEB0660-1R0MV

Table 4: Inductor Selection
2.1.3 BUCK power supply - output filter capacitor selection
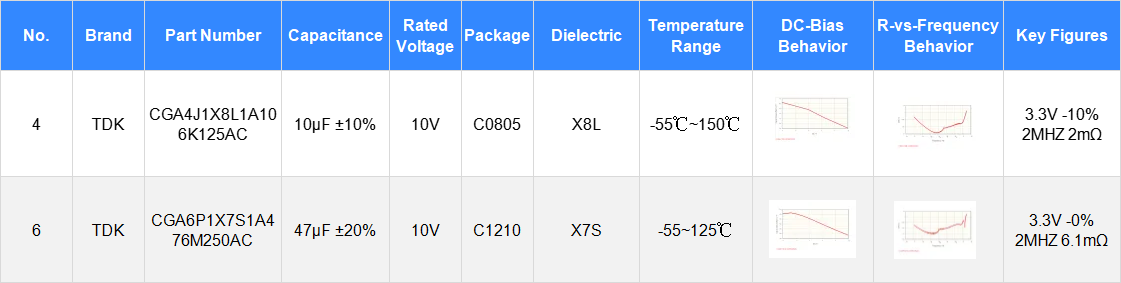
Table 5: BUCK power supply - output filter capacitor selection
2.1.4 BUCK power supply-input filter capacitor selection

Table 6: BUCK power supply - input filter capacitor selection
2.2 Schematic and PCB design tools design
2.2.1 Schematic and PCB design: Caritron EDA (https://lceda.cn/)
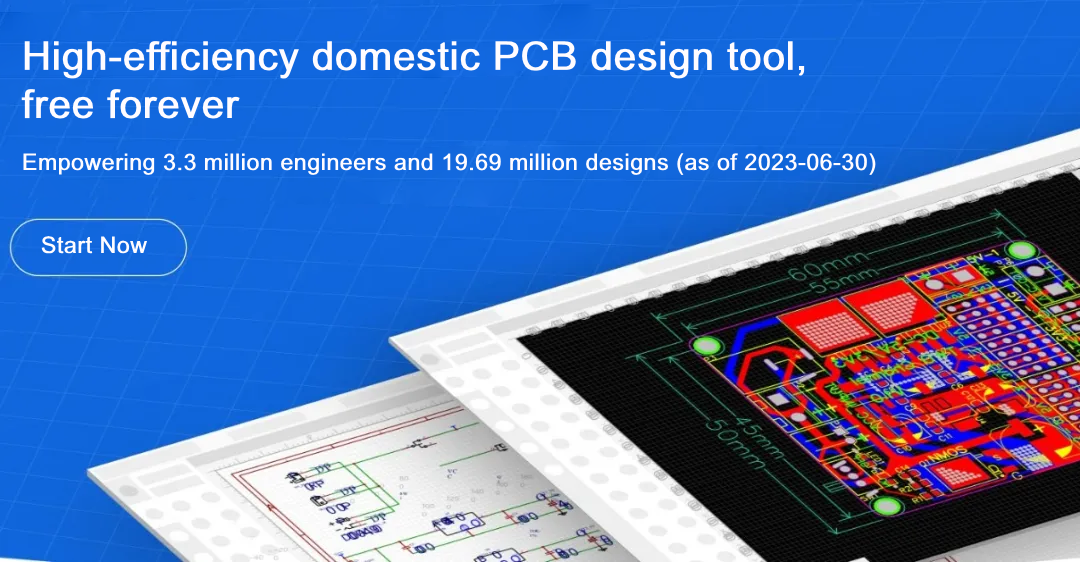
Figure 1 Introduction to Caritron EDA
Jialitron EDA is a leading free EDA development tool, powerful and efficient development, this design uses Jialitron EDA to design the schematic and PCB.
2.3 BUCK power supply-schematic design
2.3.1 BUCK power supply-schematic design
The schematic design refers to the LM25149-Q1 datasheet and the official development board, and the design conforms to the basic theory of BUCK switching power supply and the first-level power supply design requirements of high-pass domain controller.
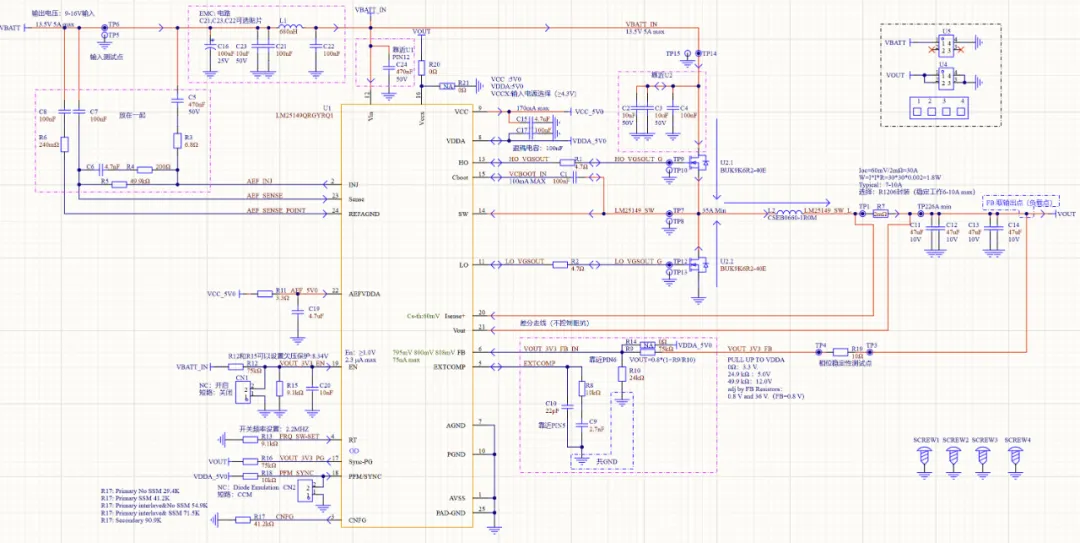
Figure 2 LM25149 Schematic
2.3.2 BUCK Power Supply - Schematic Design Focused Technology
Input port EMC circuit:
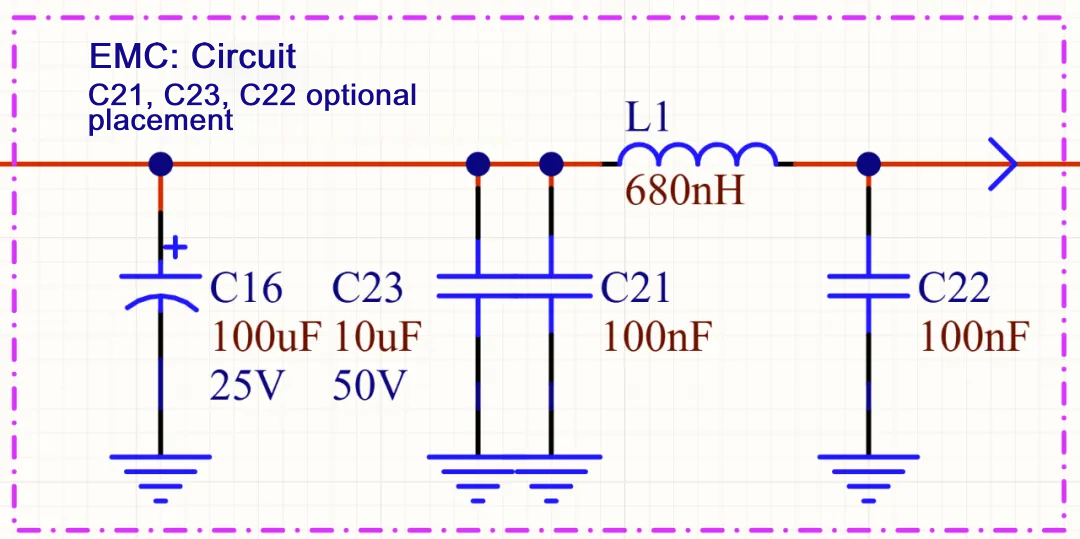
Tech Points:
① L1's main role is to reduce the impact of the switching power supply conduction radiation noise on the input power supply, switching power supply switching frequency of 2.2MHz, L1 and C23 composed of LC filter circuit (C16 is an electrolytic capacitor to 500KHz below the low frequency), 2.2MHz to reduce 60dB.
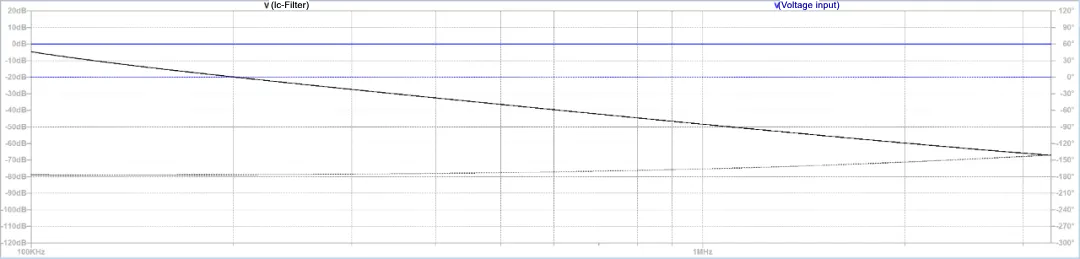
② C21 reduces switching noise (power tube rising and falling edge ringing) and mainly reduces EMC noise from 10-100MHz.
③ C21, C23 if a power supply (before protection), you need to select the flexible terminal capacitor type, if it is protected, you can choose the car specification capacitors. Can also use two capacitors in series orthogonal layout to achieve a similar protection mechanism.
For power MOSFETs and LM25149 input capacitance decoupling capacitance has the same requirements, this design is not used for performance verification, the use of a single ceramic, product-level design to follow the automotive-grade design requirements.
Note: LM25419 active EMC elimination and double random spread spectrum technology, only to a certain extent to reduce the EMC amplitude, and can not eliminate the EMC, for the switching frequency of 2.2MHz related to the energy, high-current (≥ 10A) above the application of the risk of exceeding the standard, to be based on the actual debugging, if the removal of the C23 can still be radiated through the conduction can be saved by the application of the C23, the Reduce the cost.
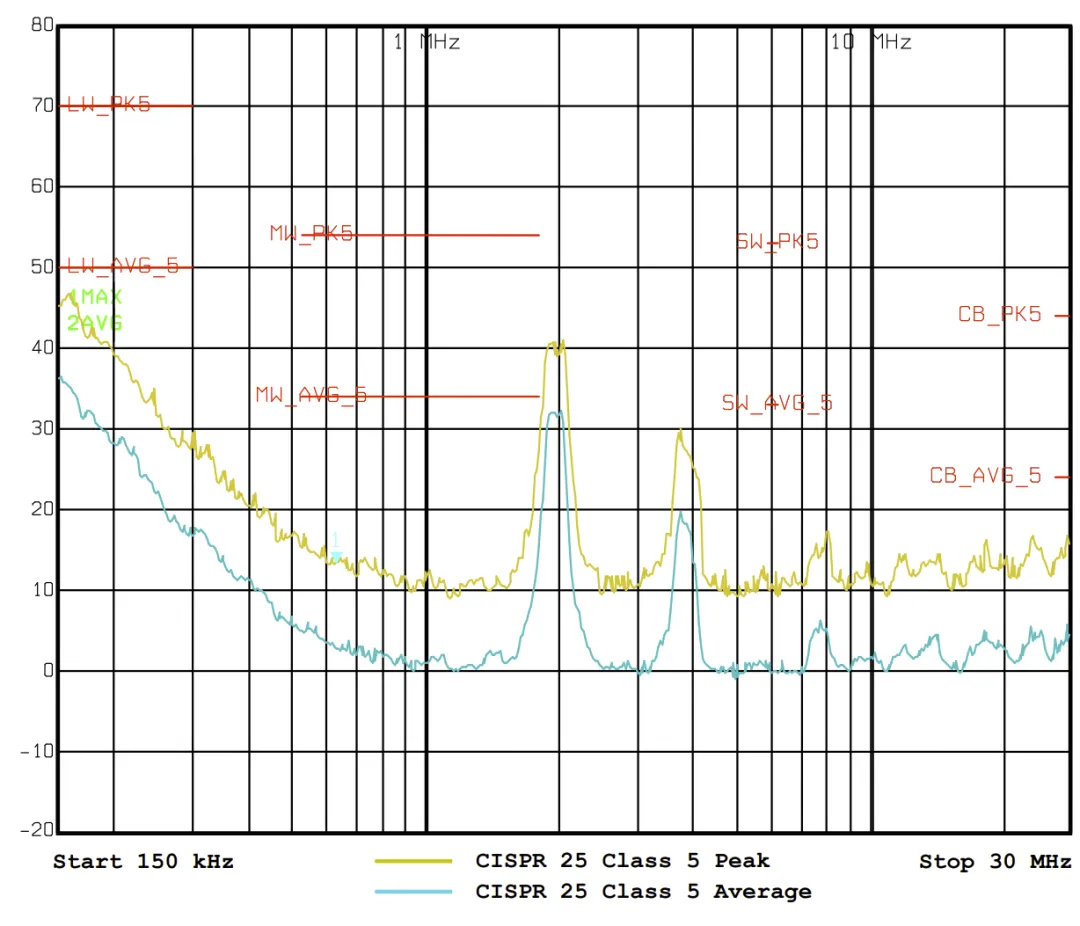
BUCK power input capacitors:
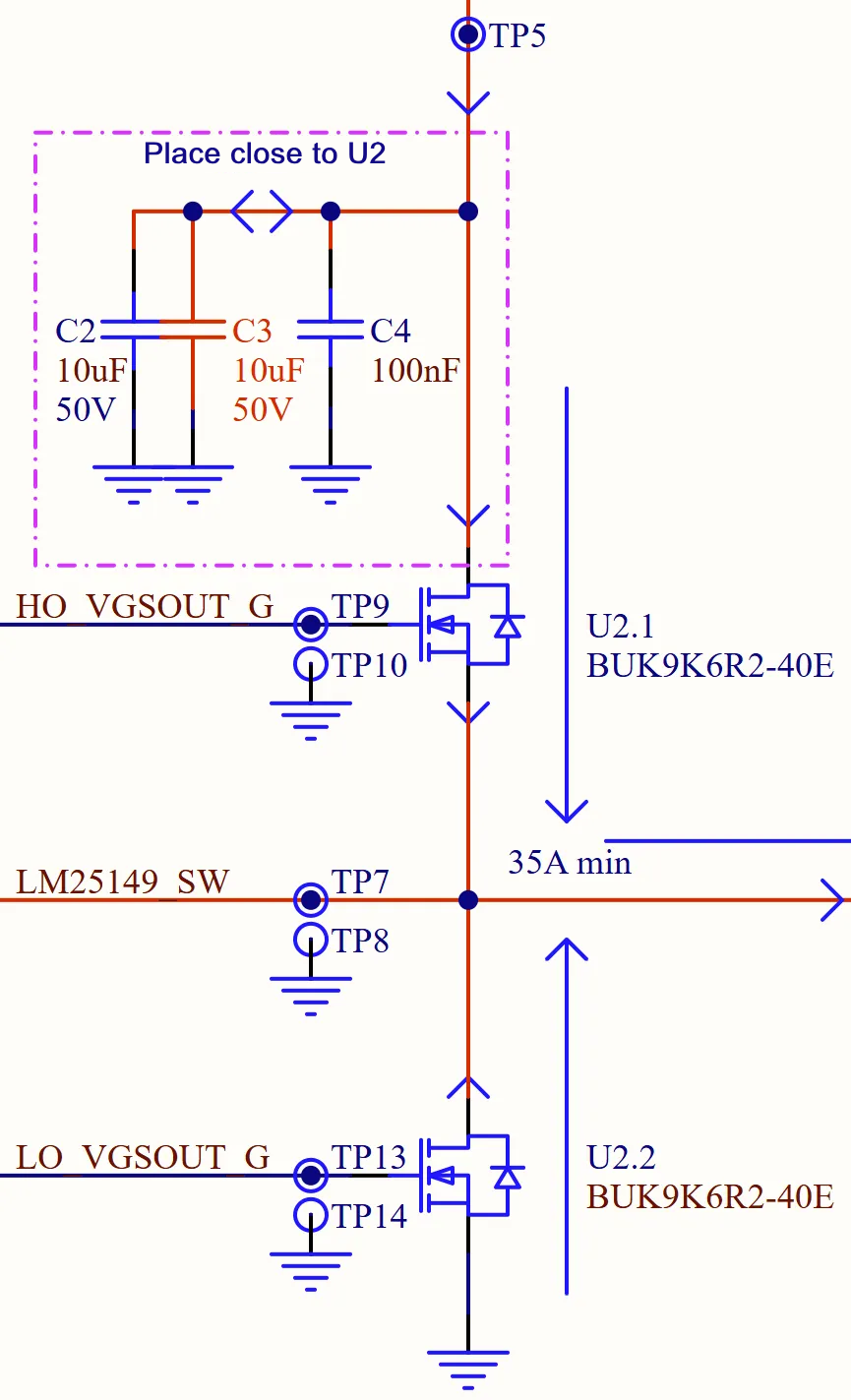
① C2,C3 for the BUCK power input capacitance, for the switching power supply EMC performance is critical, 10uF capacitance selection 2Mhz near the impedance ≤ 5mΩ, CGA4J1X8L1A106K125AC and CGA6P1X7S1A476M250AC has good technical specifications for reference, capacitance selection can be selected X7R, 35V/50V Withstand voltage, package C1210 and C1206 can be. This design selection C1210 package, you can have more models to verify the performance.
② C4 for high-frequency switching EMC capacitors, choose 50V X7R, C0402 package can be.
C2, C3, C4, Layout need to pay attention to the current loop (refer to Layout details), in line with the basic BUCK power input capacitance requirements and design theory, you can learn BUCK switching power supply theory to deepen the understanding of the input capacitance.
③ TP7,TP9,TP13 used to test the switch TG, BG and SW signals, used to test the dead time reasonableness, ringing performance, and MOSFET rising edge and falling edge performance, is an important switching power supply electrical performance test indicators.
The TP test point of GND is used to reduce the oscilloscope test GND loop and improve the test accuracy, and the LAYOUT needs to be placed as close as possible to the test point of the relevant test signals.
MOSFET gate drive resistor:
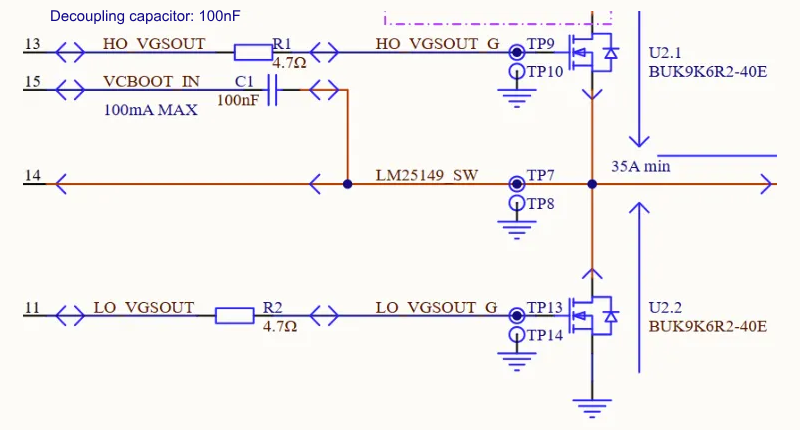
① R1 and R2 are MOSFET gate drive resistors, which have an important effect on the rising and falling edges of the power MOSFET.
② R1, R2 selection is controlled by the BUCK power controller output current (controller (PULL and PUSH resistors), power MOSFET gate impedance and charge characteristics (input capacitance CISS) comprehensive reasons for the impact of the initial design selection of the entire resistor sum of ≤ 10 ohms, but also depends on the charge characteristics, the need for eventual fine-tuning, the choice of the appropriate resistance value.
③ R1 and R2 is also the switching noise EMC most critical parameters, while affecting the switching loss of the core circuit factors, in practical applications need to balance the efficiency (MOSFET heating) and EMC contradictions to achieve a balance point.
Note: 6 test points for testing the switching characteristics and dead time.
Output power loop:
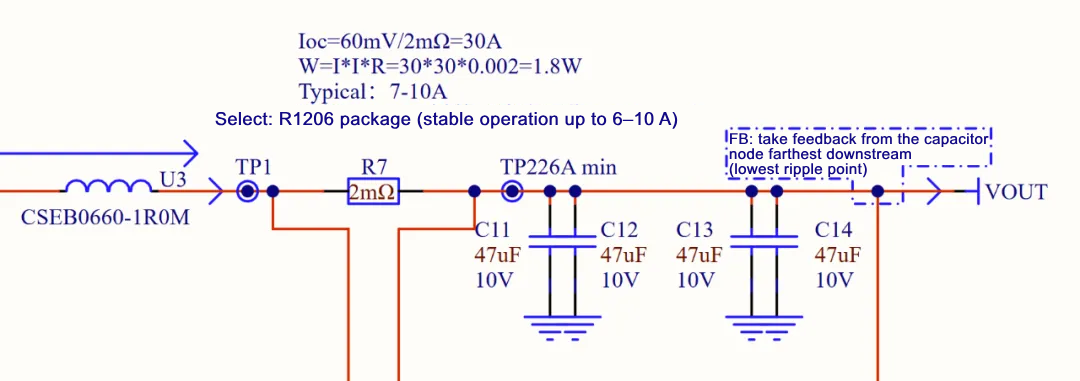
① Inductance selection: Inductance selection is based on two main considerations:
-Transient operating current: able to transient output 21 (24) A (time: 100us);
-Steady state operating current: 10A, able to work stably at 10A current (covering 85° ambient temperature conditions);
-Transient operating current duration ≤ 100us, and occurs in the start-up phase, only need to ensure that the inductor does not saturate the conditions to meet the requirements (to meet the current inductance value).
② Sampling resistor selection: sampling resistor selection R1206 package, thermal power dissipation ≥ 0.5W;
③ Selection of capacitors: reference: the first part of the chapter output filter capacitance chapter;
Feedback Circuit:
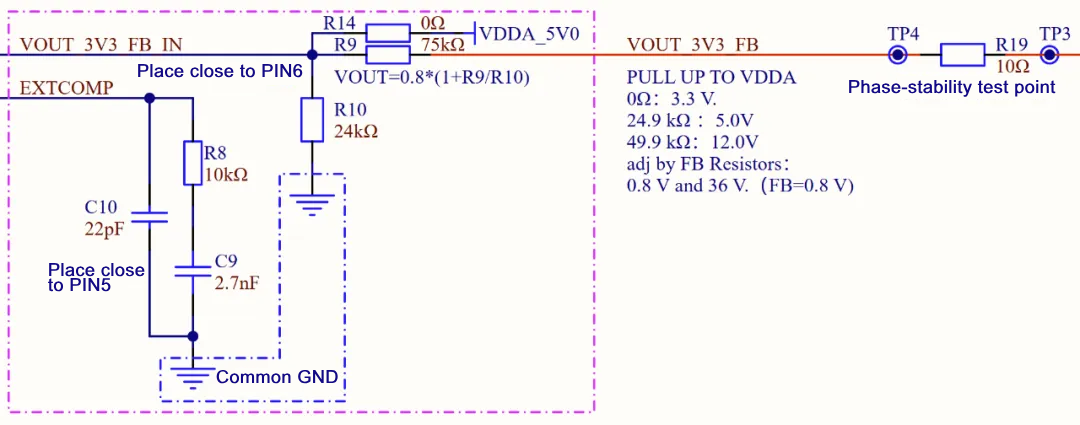
The LM25149 has a fixed output configuration and a feedback output configuration, refer to the datasheet for details;
① R14l connected to VDDA, output 3.3V
② R14=24.9K, output 5.0V
③ R14=49.9K, output 12.0V
Empty paste R14, R9 and R10 configure the output voltage;
R19 and reserved TP3, TP4: for testing, phase margin, crossing frequency, etc.
Note: TP3 and TP4 are used for testing, phase margin, crossing frequency, etc.
Function Setting:
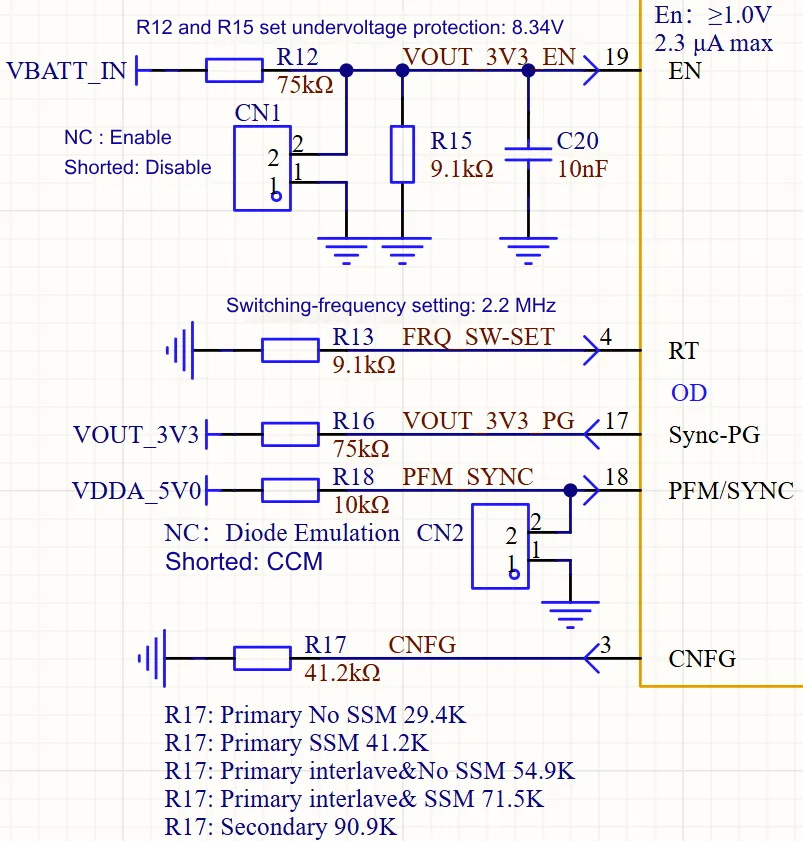
① EN: Enable signal, ≥1.0V turn on the power, can be used for precision undervoltage protection;
② Sync-PG: Synchronous output or Power good, this design is used for Power good;
③ PFM/SYNC
-Default (NC) jumper: Diode analogue, small current output, can work in high efficiency;
-Short circuit jumper to GND, force CCM mode;
④ Chip operating mode settings: a total of five operating modes (refer to the specification)
2.4 BUCK power supply-PCB design
2.4.1 BUCK power supply-PCB design
① -TOP
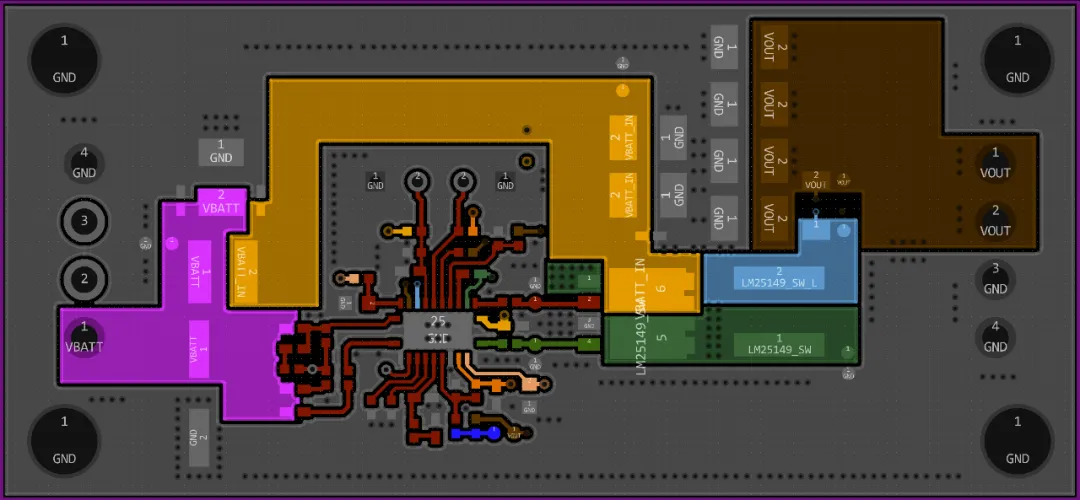
② -GND
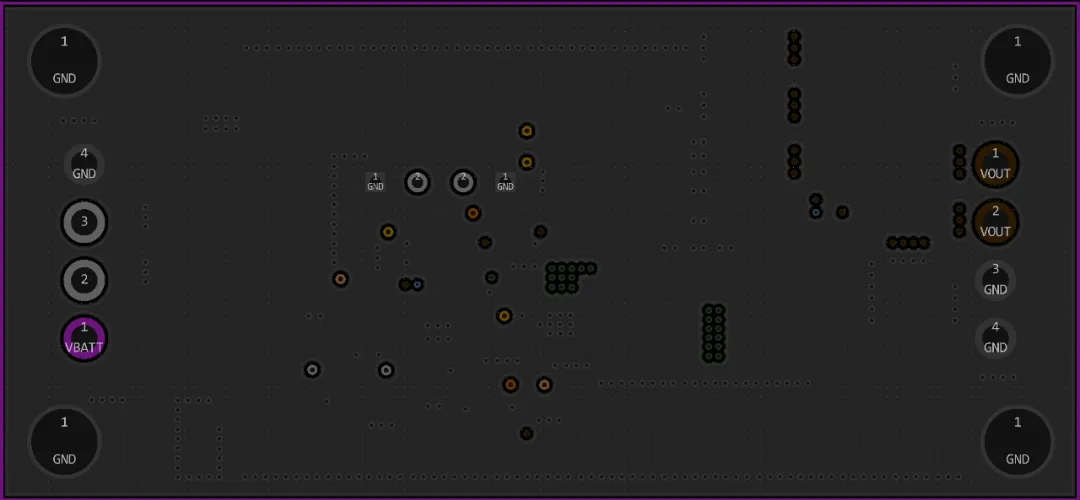
③ -Signal
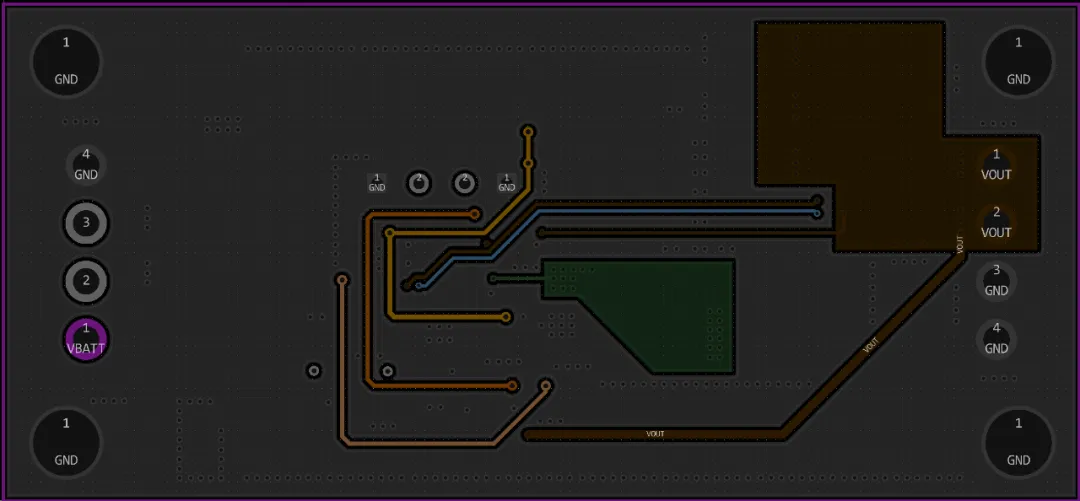
④ -Bottom
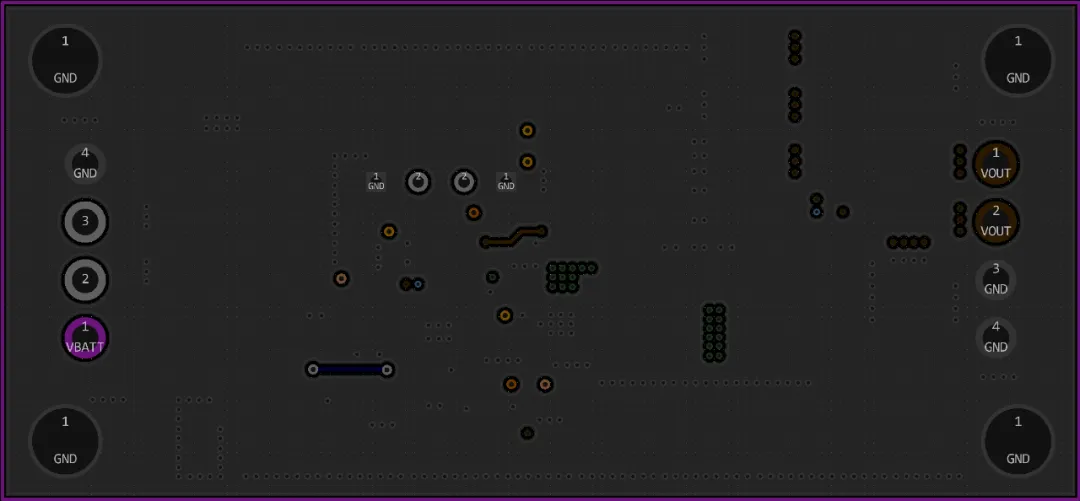
2.4.2 BUCK power supply-PCB design focus on technology
Input and output capacitance loops:
① BUCK power supply input capacitance and output capacitance to maintain a minimum loop, has an important impact on EMC;
② C4 is mainly used to absorb switching rising and falling edge ringing noise.

MOSFETs and inductive loops:
① The use of two-in-one MOSFETs reduces the layout area and lowers the cost, but the disadvantage is that the Layout SW cannot maintain the minimum loop;
② The SW point of the two-in-one MOSFET can't realise the same layer of PCB alignment, and it needs to change the layer to pave the plane in order to realise the continuity of power current.
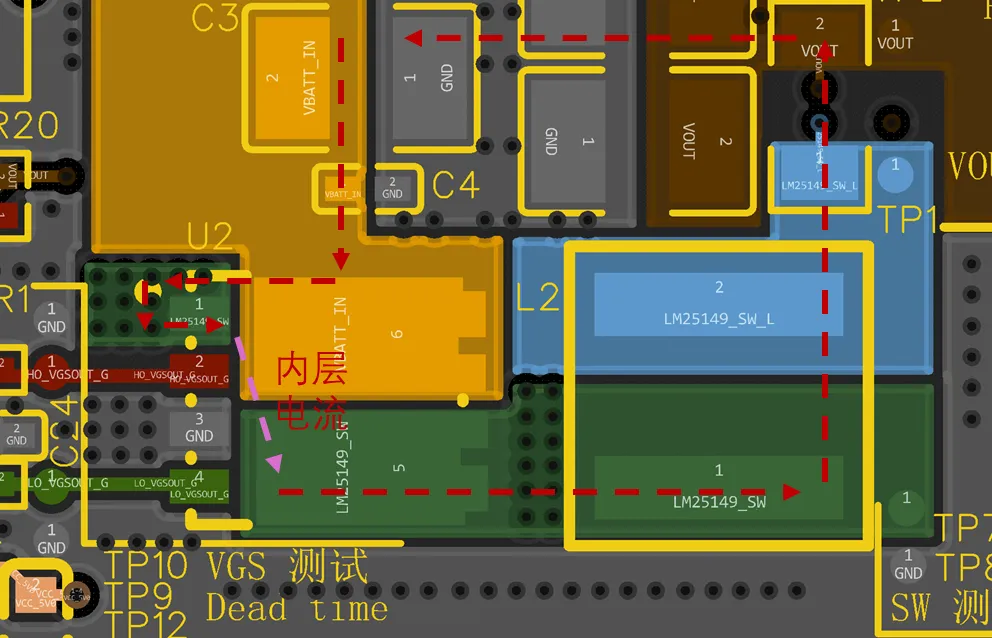
Sampling current:
① Sampling current requires a differential alignment with a reference GND plane;
② Impedance control and equal length are not required, and the alignment maintains Layout minimum spacing.
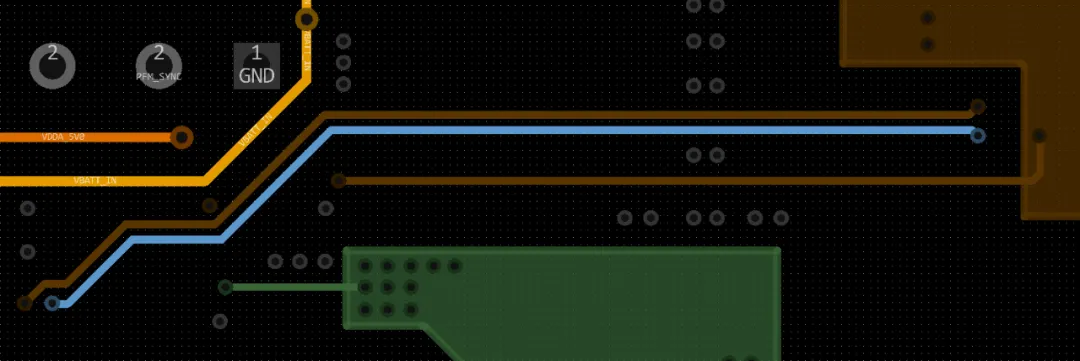
FB Feedback:
Resistors and other devices are close to the control chip pins.
Heat dissipation and GND:
Heat generating devices: MOSFETs, inductors and sampling resistors, you can appropriately increase the plane area to conduct heat, and increase the GND perforation can help to improve the heat dissipation conditions of the whole version.
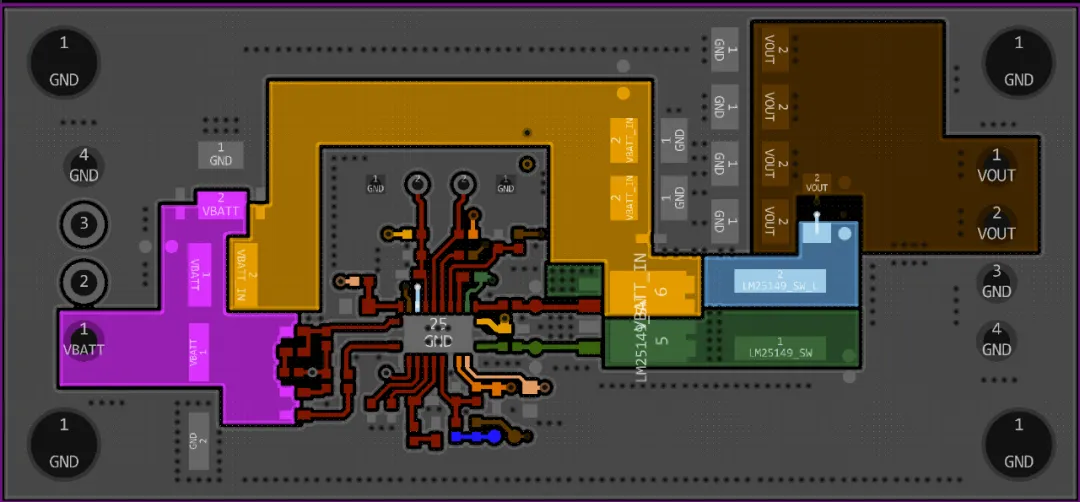
3- Domain Controlled Level 1 BUCK Power Supply Design - Summary
3.1 3D Drawing
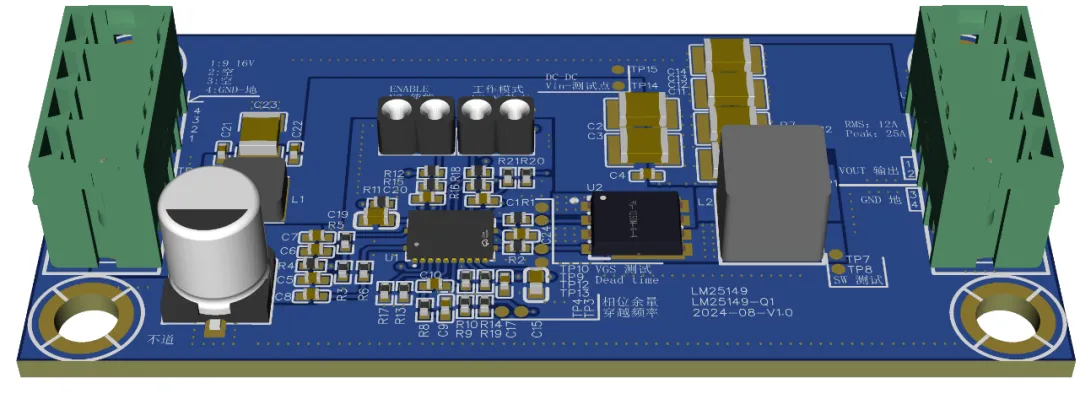
3D Figure-1

3D Figure-2
3.2 Design Summary
① The switching power supply design adopts a 4-layer design with a PCB thickness of 1.6mm and a size of 30X65mm;
② The output current can meet Qualcomm SA8295 maximum 24A transient current, support steady state 10A or more output capability.
4- About Codaca Electronics
Codaca focuses on inductor independent R&D, design and manufacturing, VSEB0660-1R0M is suitable for Qualcomm platform development and application. It has the technical advantages of high cost performance, high resistance to saturation current, low heat generation, and industry-leading power-to-volume ratio. Codaca focuses on technology research and development, technological innovation, research and development of excellent products for the inductor industry, to help the development and application of electronic products.
5- Test and Verification
For follow-up test verification, please refer to: 03-Deciphering Qualcomm's Automotive Domain Controller Level 1 Power Supply Design: Performance Test Measurement Analysis (to be released)
[Reference]
1.LM25149-Q1:ti.com.cn/product/cn/LM25149-Q1
2.BUK9K6R2-40E:https://www.nexperia.cn/product/BUK9K6R2-40E